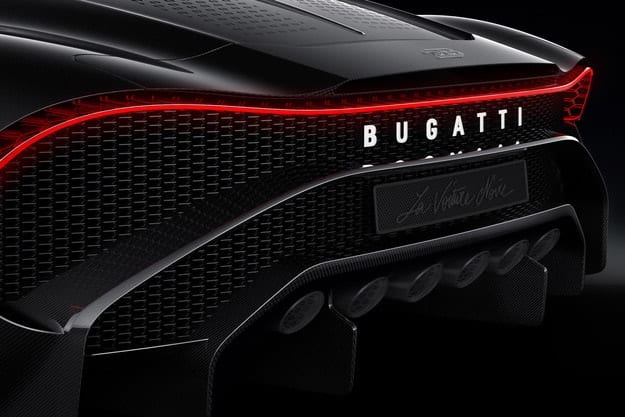
Bugatti: Pag-print ng 3D sa gitna ng Chiron
Ginagamit ng tagagawa ng Pransya ang teknolohiyang ito sa 2018 para sa modelo ng Chiron Sport.
Mula noong 2018, ang tagagawa na nakabase sa Molsheim ay gumagamit ng 3D na teknolohiya sa pag-print upang makagawa ng ilang mga bahagi ng Chiron hypersport, tulad ng mga tip ng tambutso ng titanium ng mga modelo ng Pur Sport at Super Sport 300+.
Tulad ng Ettore Bugatti, tagapagtatag ng tatak ng tricolor na regular na nagpapakita ng mga makabagong ideya sa disenyo ng mga modelo nito (pangunahin naming utang sa kanya ang mga haluang metal na gulong at guwang sa harap ng ehe), ang mga inhinyero na responsable para sa pagbuo ng mga bagong modelo ng Bugatti ay may kasamang pinakabagong mga pagbabago. sa konstruksyon o engineering sa kanyang mga nilikha. Ang teknolohiya sa pag-print ng 3D, ang mga benepisyo na kilalang kilala, ay isa sa mga ito.
Ginamit ng Bugatti ang teknolohiyang ito noong 2018 sa Chiron Sport, na pagkatapos ay nilagyan ng mga tip sa tambutso na gawa sa Inconel 718, isang matigas at magaan na haluang metal na nickel-chrome lalo na ang lumalaban sa init (sa kasong ito, natutunaw ang aluminyo). Ang mga susunod na modelo ng tatak (Divo, La Voiture Noire, Centodieci…) ay makikinabang din mula sa proseso ng paggawa na ito para sa kanilang mga tailpipe.
Ang mga 3D na naka-print na elemento ay may maraming mga pakinabang. Sa isang banda, ang mga ito ay higit na lumalaban sa init at tinatanggal ang build-up ng init na nilikha ng 8,0-litro na W16 1500 hp engine, at mas magaan din kaysa sa maginoo na mga iniksyon. (Ang Chiron Sport ay may bigat na 2,2 kg lamang, halimbawa 800 g mas mababa sa isang maginoo na iniksyon).
Sa kaso ng bagong Chiron Pur Sport, gumagawa ang Bugatti ng mga 3D na naka-print na titanium exhaust nozzles, at ipinahiwatig ng tagagawa na ito ang "ang unang nakikitang bahagi ng metal na nakalimbag sa 3D na may homologation ng trapiko sa kalsada." Ang pagkakabit na ito ay 22 cm ang haba at 48 cm ang lapad at may bigat lamang 1,85 kg (kabilang ang grill at maintenance), na halos 1,2 kg na mas mababa sa "standard" na Chiron.
Ang isang espesyal na sistema ng pagpi-print ng laser na ginagamit para sa pag-print ng 3D ay binubuo ng isa o higit pang mga laser, na kung saan natutunaw ang mga layer ng alikabok sa pagitan ng 3 at 4 na microns na laki. 4200 mga patong ng metal pulbos na stack sa tuktok ng bawat isa at fuse magkasama upang mabuo ang Chiron Pur Sport outlet nozzle na makatiis ng temperatura sa itaas ng 650 degree Celsius, habang nagbibigay ng pagkakabukod ng thermal sa mga katabing bahagi salamat sa dobleng panlabas na pader.
Ang mga sangkap na ito ay sa wakas ay espesyal na pinahiran bago maingat na suriin at mai-install sa sasakyan. Halimbawa, ang Chiron Sport ay may buhangin sa corundum at may lacquered na itim na may mataas na temperatura na ceramic na pintura, habang ang Chiron Pur Sport at Super Sport 300+ ay magagamit sa isang matte na titanium finish.
Sa pamamagitan ng paggarantiya ng tibay, ultra-gaan at estetika ng mga bahagi, ang teknolohiya sa pag-print ng 3D, na hanggang ngayon ay pangunahing ginagamit sa aeronautics at space, tila sa wakas natagpuan ang lugar nito sa mga tagagawa ng kotse, kahit na ang pinaka-hinihingi.
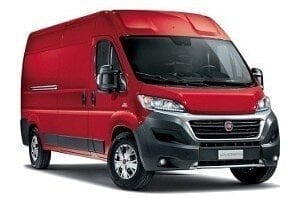
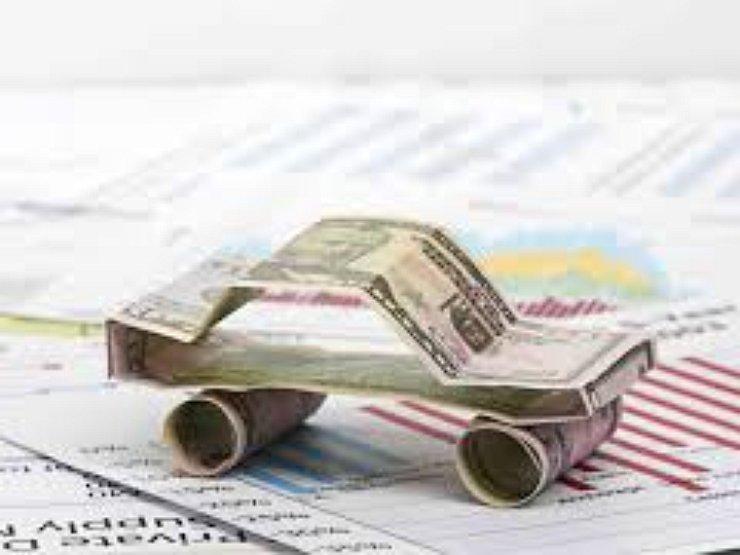